Inspection optique automatique des couches internes (AOI)
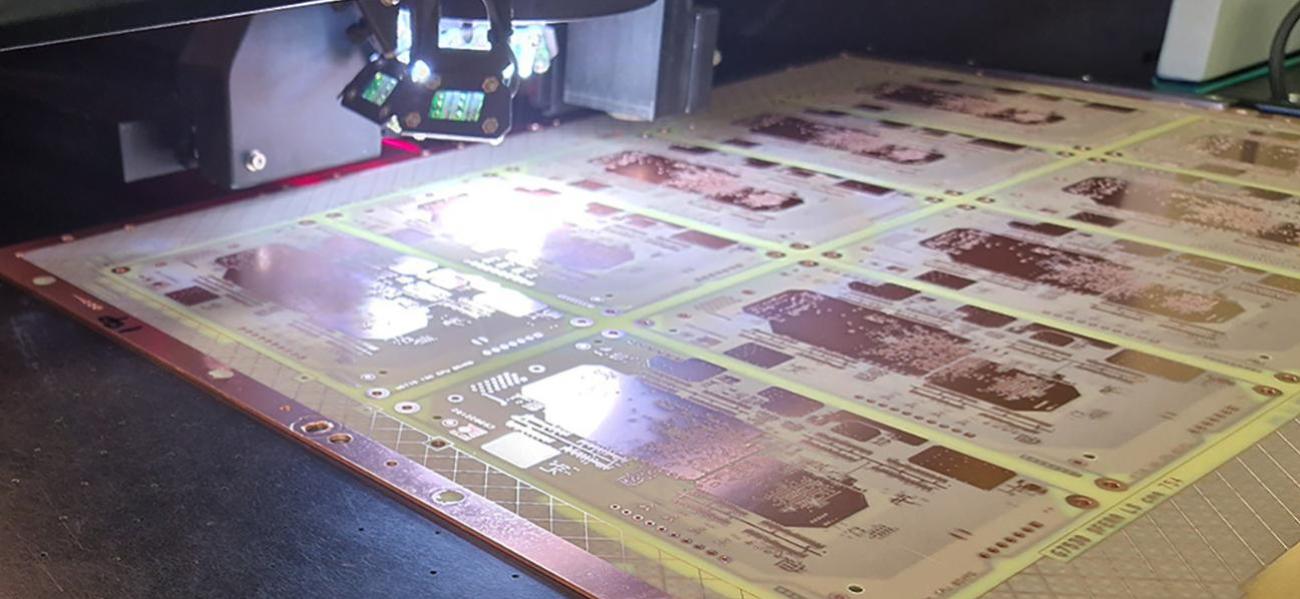
Même si ça ne suffit pas, nous savons tous que «Bien commencé est à moitié fait !».
Combiner la maîtrise statistique des procédés (MSP) et l’inspection optique automatique contribuerait à faire démarrer au mieux le processus de production d’un circuit imprimé et à apporter des améliorations itératives le cas échéant.
Dans notre dernier article, nous avons décrit le processus de gravure des couches internes, du développement du film sec à la gravure du cuivre, en passant par le strippage du film sec résiduel pour obtenir une couche interne gravée, prête à prendre part à l’empilage du circuit imprimé.
Comme indiqué précédemment, pour optimiser le résultat de ce processus, il est nécessaire que les conditions du processus de gravure lui-même et les conditions des processus précédents de laminage des couches internes et d’impression par reproduction photographique restent stables.
Ensuite, le bon sens, avant même les obligations dictées par les normes IPC, suggère d’inspecter les couches internes gravées. Cependant, selon les normes IPC, les couches internes doivent être entièrement inspectées après le processus de gravure acide.
D’un point de vue pratique, l’AOI est une comparaison entre la conception de la couche interne et la véritable couche interne après le processus de gravure acide. Pour ce faire, il faut charger dans la machine AOI le dessin de la couche interne à inspecter et les tolérances d’acceptabilité sur les différentes géométries telles que les pastilles, les pistes, l’espacement, les résistances intégrées et les profils (en particulier en cas de structures micro-ondes).
Le service outillage est chargé de fournir le dessin au service AOI pour lui permettre d’effectuer l’AOI.
Le processus AOI est basé sur des règles d’acceptabilité normalement définies dans un plan de contrôle. Ce document contient les exigences/spécifications du client et/ou d’autres normes adoptées dans le secteur des circuits imprimés.
Ci-après une liste des spécifications les plus courantes utilisées dans le monde entier :
- IPC-A-600
- IPC 6012 pour circuits imprimés rigides, IPC 6013 pour circuits imprimés souples et flex-rigides, et IPC 6018 pour circuits imprimés haute fréquence et micro-ondes.
- Addendum spécifique IPC pour les secteurs critiques tels que l’espace, l’automobile et le médical
- ECSS-QC-ST-70-60C pour les applications dans le secteur spatial.
Cette inspection a pour but d’identifier toutes les non-conformités afin de suggérer les ajustements à apporter aux processus de laminage et de photogravure de la couche interne jusqu’au processus de gravure acide. Ces corrections permettront de réduire les non-conformités et, le cas échéant, de les identifier le plus rapidement possible afin d’éviter de perdre du temps et de l’argent dans la production d’un circuit imprimé « non conforme » dès le départ.