Préparation et pressage de l’assemblage
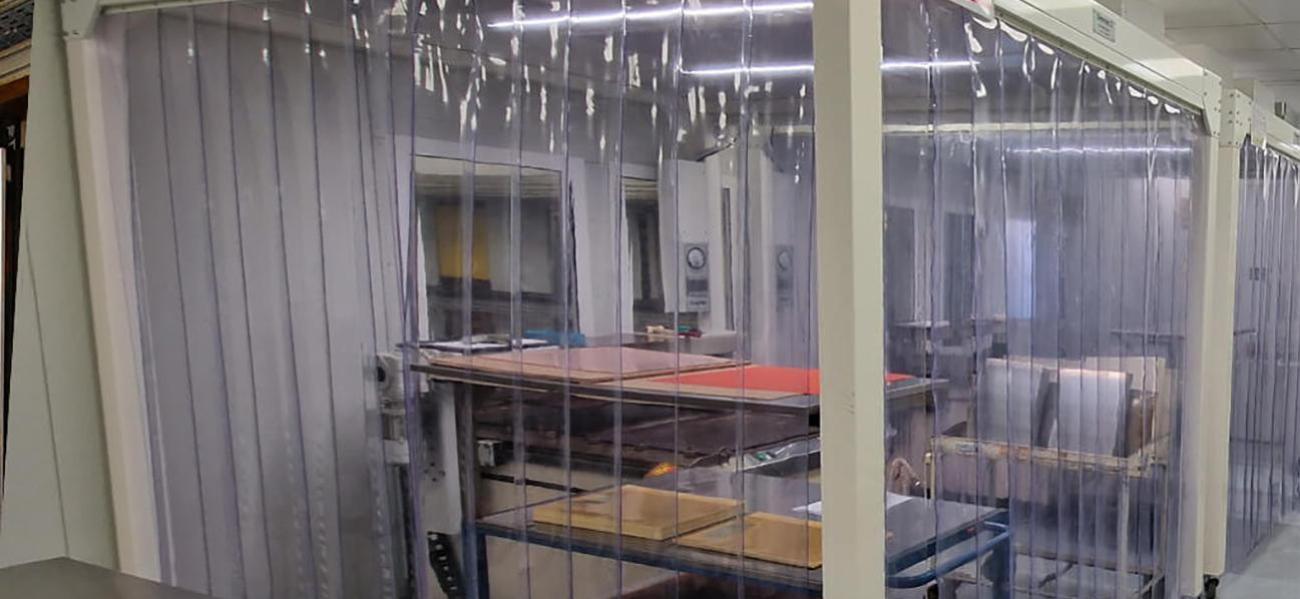
Vous êtes toujours là ?
Alors montez donc à bord pour poursuivre notre voyage à la découverte du processus de fabrication d’un circuit imprimé multicouches.
Nous sommes tout juste après le processus de brunissage (black-oxide), nous avons entre les mains toutes les couches internes nécessaires déjà poinçonnées, noircies et séchées, prêtes donc à être empilées et pressées avec les couches de pré-imprégné pour obtenir, à l’issue de la phase de pressage, un panneau solide, la base de ce qui deviendra un ou plusieurs circuits imprimés finis.
Le pré-imprégné est l’un des matériaux les plus importants pour la production de circuits imprimés, avec les laminés et la feuille de cuivre.
Le pré-imprégné représente la «colle» nécessaire pour maintenir ensemble, tout en les isolant les unes des autres, les différentes couches internes et les deux couches externes incluses dans l’empilage (stake-up).
Une couche de pré-imprégné est en fait une « feuille » constituée d’un tissu de fibre de verre pré-imprégné de résine thermodurcissable, du même type que celle de chaque couche interne adjacente.
Le pré-imprégné est généralement FR4, à savoir «flame retardant 4», mais, comme nous l’avons déjà expliqué pour les couches internes, le type de résine et les fibres de verre peuvent avoir des caractéristiques différentes qui confèrent à chaque circuit imprimé des propriétés mécaniques et électriques adaptées à chaque application spécifique.
Pour bien choisir votre fournisseur de circuits imprimés, il est bon de vous assurez qu’il est capable de travailler avec une large gamme de matériaux afin de vous aider de manière adéquate quelle que soit l’application spécifique de votre circuit imprimé.
À noter que les différents matériaux peuvent se dilater ou se rétracter différemment en fonction de la température, ce qui peut entraîner une mauvais interconnexion des couches internes ainsi que le délaminage au niveau des interfaces cuivre-substrat.
Par conséquent, pour presser des matériaux différents ou, plus encore, pour presser des matériaux mixtes, il est nécessaire de valider et d’adopter des cycles température-pression spécifiques.
Le choix du bon cycle température-pression pour le pressage des PCB, qui comporte également la définition de la vitesse permettant d’atteindre les valeurs maximales de température et de pression ainsi que de la période de temps pendant laquelle ces valeurs doivent rester stables après avoir été atteintes, est une question très critique.
Chaque résine - à savoir la résine incluse dans les couches internes ainsi que la résine présente dans le pré-imprégné - a en effet sa propre température de transition vitreuse (Tg), qui est la température à laquelle un système polymère devient un matériau amorphe et visqueux, comme le verre fusionné.
En effet, à la température Tg, les chaînes polymériques acquièrent la « liberté » de se déplacer : la résine des couches internes peut adhérer à la résine du pré-imprégné, avec laquelle elle peut également se combiner, et au cuivre resté sur les couches internes après la gravure, de manière à générer un bloc unique.
À noter en outre que les différents pré-imprégnés ont des teneurs en résine différentes et que les résines différentes les unes des autres ont des capacités différentes à « s’écouler » lorsque la Tg relative a été atteinte.
Par conséquent, le pourcentage de résine dans le prépeg et sa capacité à s’écouler est un autre paramètre important à contrôler afin de garantir un couplage idéal avec les couches internes. En effet, si d’une part le pourcentage de cuivre (copper percentage) encore présent sur les couches internes après gravure peut varier considérablement en fonction de la conception du circuit imprimé, d’autre part il est important d’éviter que la résine n’atteigne et ne colle certaines parties des circuits imprimés, telles que les couches souples dans les circuits imprimés Flex-rigides.
En outre, le prépeg doit être défini avec une extrême précision pour les circuits imprimés comportant des «pistes à impédance», où la combinaison de l’épaisseur de l’isolation et des dimensions des pistes détermine les valeurs d’impédance.
Enfin, il ne faut surtout pas oublier que la phase de pressage s’effectue sous vide, ce qui est nécessaire pour éviter de laisser des «vides» dans les circuits imprimés, qui pourraient ensuite être à l’origine d’une délamination lors de la refusion pendant le montage en surface (SMT).
Il est donc important, pendant le processus de laminage, de gérer certains paramètres de base:
- l’augmentation de la température, tant pour le chauffage que pour le refroidissement
- l’augmentation de la pression, en une ou plusieurs étapes
- les valeurs de vide
- le temps nécessaire pour chaque étape de pressage.
Toutes ces valeurs doivent être enregistrées pour assurer un contrôle et une traçabilité adéquats du processus.
Enfin, ce qui n’est d’ailleurs pas le moins important, pour produire des circuits imprimés fiables, il faut garantir des conditions de propreté extrême.
C’est pourquoi, dans la zone de pressage, et en particulier pendant la phase de montage, il est nécessaire d’utiliser des procédures, des instruments et des systèmes spécifiques pour la filtration et le traitement de l’air afin d’éviter les risques de contamination par des «corps étrangers».