Statistische Prozesskontrolle in der Leiterplattenfertigung
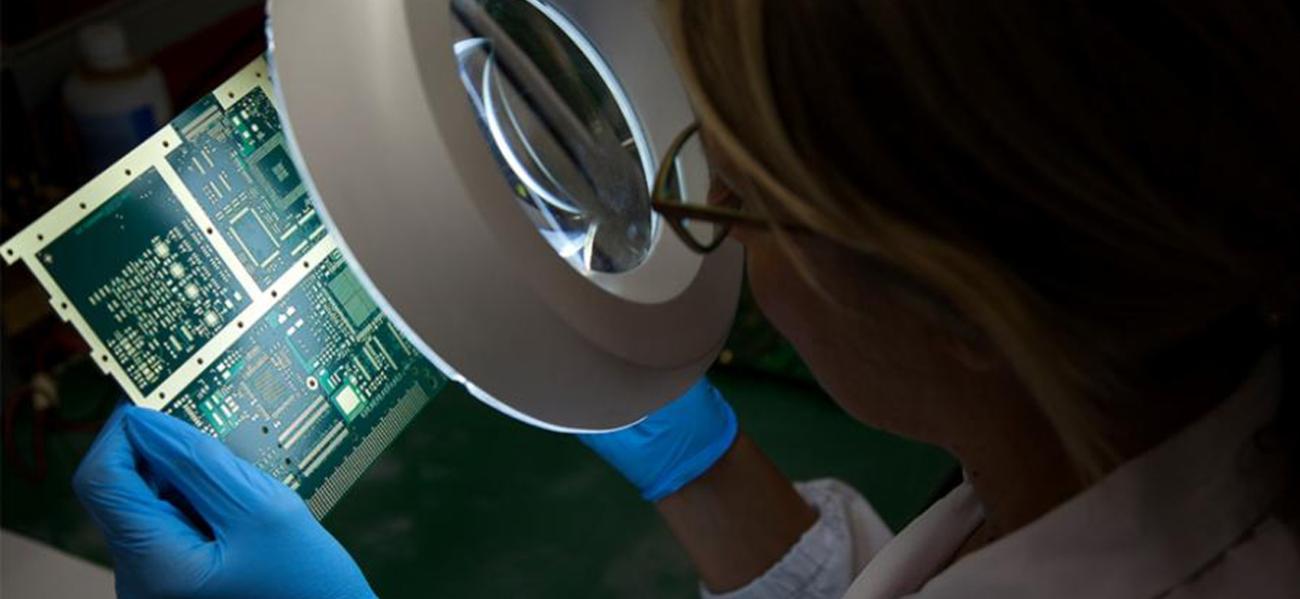
Qualität wurde als messtechnische Kontrolle des Produkts geboren und dieses Konzept entwickelte sich in den 90er Jahren als Grundlage der ersten Versionen der zertifizierbaren Norm ISO 9001.
Im Laufe der Zeit haben die Standards jedoch die nicht nur wirtschaftliche Möglichkeit aufgezeigt, das Niveau der Qualitätskontrolle, verstanden als „Autopsie von Teilen außerhalb der Toleranz“, zu verringern, indem sie eine Reihe von Logiken implementieren, die den Fokus vom Produkt auf den Prozess verlagern –mit einem präventiven Ansatz in Bezug auf den Zeitpunkt der Produktion.
EPN hat seit mehreren Jahren die statistische Kontrolle der Prozessvariablen übernommen und das interne Labor überwacht ständig den Trend der Hauptwerte durch über 60 Prozessanalysen, von denen die Trends und historischen Werte der Kapazität bekannt sind.
Diese Logik, ähnlich derjenigen, die für die Validierung spezieller Prozesse verwendet wird (d. h. Prozesse, bei denen die Ergebnisse des Prozesses nicht direkt messbar sind), verwendet fortgeschrittenere Formen der Statistik als die klassische Qualitätskontrolle, die sich auf die Überprüfung der Kapazität des Prozesses konzentrieren, als statistischer Ausdruck des Leistungsniveaus in Bezug auf die von den Produktspezifikationen geforderte maximale Toleranz.
Die Studien basieren auf der Normal- oder Gaußschen Verteilung, um zu überprüfen, ob die Art und Weise, in der die Werte der gemessenen Probe unter Anwendung der Normalitätshypothese derselben eine Prozesskurve darstellen, die mit dem für diesen Wert erwarteten Toleranzbereich kompatibel ist.
Auf diese Weise kann das System im Gegensatz zur klassischen Messung, die bestimmt, ob eine Reihe von Werten innerhalb der vorgegebenen Toleranz liegt oder nicht, die Wahrscheinlichkeit ausdrücken, mit der die Prozesswerte innerhalb der Toleranzgrenzen liegen und um den möglichen Prozentsatz von Produkten vorherzusehen, die dieser nicht entsprechen.
Wenn wir uns dem Bereich der Statistik zuwenden, können wir, obwohl wir einen populären Ansatz beibehalten wollen, sagen, dass die Indizes, die diese Verhaltensweisen darstellen und beschreiben, insbesondere Cp und Cpk sind.
Anschaulich können wir definieren, dass Cp die Breite der Gauß-Kurve um den Mittelwert herum beschreibt, während Cpk die Zentrierung des Prozesses in Bezug auf die Extreme darstellt, wobei immer Cpk ≤ Cp ist.
Im folgenden Beispiel sind zwei Wertesätze von 25 Maßnahmen auf einem theoretischen Ziel von 1,5 ± 0,1 dargestellt.
Es ist ersichtlich, wie die beiden Wertereihen, obwohl beide 100 % der Messungen innerhalb der Toleranz aufweisen, Prozessfähigkeiten hervorheben, die sich von der erwarteten Messung unterscheiden, und wie für die zweite Reihe ein Prozentsatz von Ausschussteilen vorhersagbar ist.
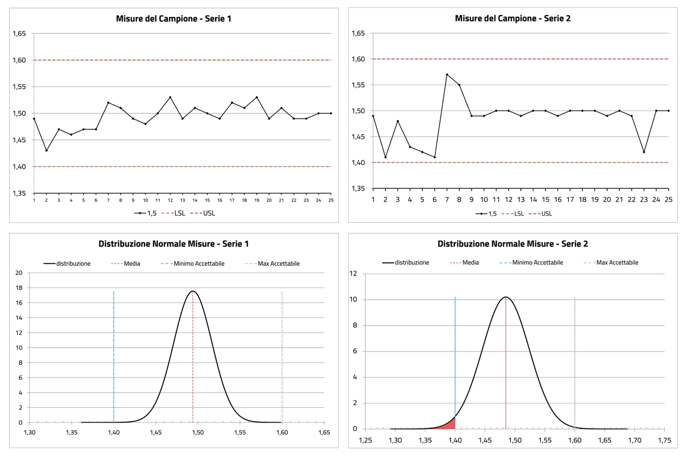
Es ist zu beobachten, dass die Kapazitätsindizes der beiden Serien unterschiedlich sind:
Series 1 | Series 2 |
Cp und Cpk > 1,33 | Cp und Cpk < 1 |
% Erwarteter Ausschuss 0% | % Erwarteter Ausschuss 2% |
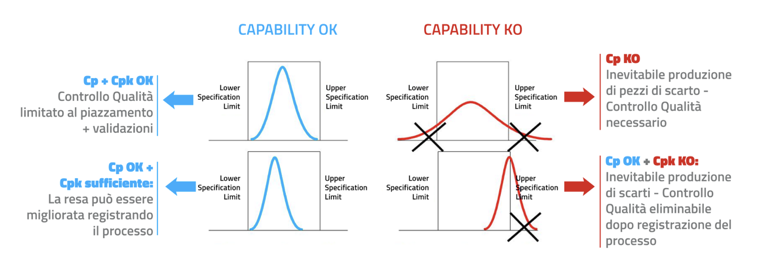
Die Kenntnis und Interpretation dieser Werte ermöglicht es, die Qualitätskontrollfrequenzen besser zu organisieren und zu verstehen, warum es nicht möglich ist, einige Kontrollphasen während der Produktion von Leiterplatten (insbesondere die automatische optische Kontrolle der Innenlagen und die elektrische Kontrolle) zu 100% zu vermeiden.
Basierend auf der Prozessanalyse können verschiedene Fälle gefunden werden:
Diese Bedingungen bestimmen differenzierte Eingriffe, um den Prozess wieder auf optimale Bedingungen zu bringen.